Talos is our newest robot. Design started early August 2022, right after competition while we were still in Maryland! The design goals for Talos were pulled from Tempest’s shortcomings. This included plans to strengthen the chassis, design a next gen electronics system: Mark II, and create hassle-free smart battery housings. Talos has now been built on the solid foundation of Tempest and is ready to strut its stuff at RoboSub 2023.
At a glance:
- 8 thrusters providing 6 degrees of freedom
- Two central housings containing vehicle electronics
- Rigid chassis built from 6061 Aluminum
- VectorNav VN-100 IMU, Nortek DVL 1000-300m, and Blue Robotics Bar02 Depth sensor
- StereoLabs Zed 2i 3D Camera using YOLOv5 for computer image detection
- Nvidia Jetson Orin as the primary vehicle computer
- Custom designed vehicle electronics
- Hot-Swappable Batteries
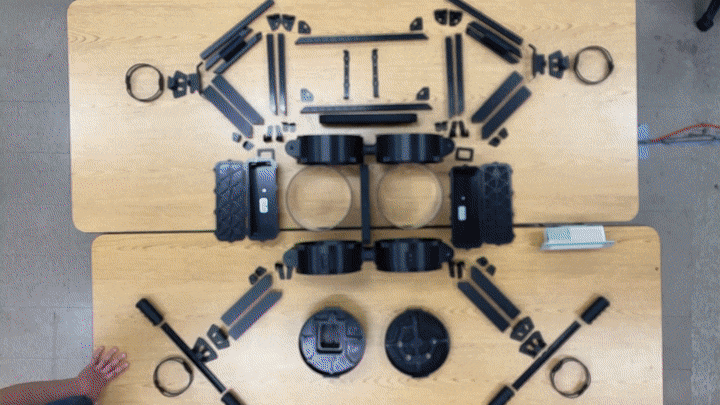
We would like to happily announce that our vehicle, Talos, has successfully completed RoboSub prequalification!
Watch our prequalification run below:
The Mark 2 electronics is the next generation electronics running Talos. These electronics were primarily developed throughout the 2022-23 academic year, taking lessons learned from Tempest’s Mark 1 electronic system to make a more reliable and polished electronics system. The electronics system underwent the following changes:
- Distributed architecture with each circuit board containing an independent microcontroller communicating over CAN Bus
- Switched the physical layout of the electronics to increase circuit board density
- Increased telemetry available from the electronics system to allow for complete system diagnostics over the network
Read more about the team’s electrical systems on the Navionics Team Page
Diagram of Mark 2 Architecture:
Talos underwent many improvements to the mechanical systems throughout the vehicle redesign. Some of these include:
- Pocketed lids to reduce weight, overall 2.7 kg lighter than Tempest
- Improved thruster cable management to reduce drag
- Electronics cages mounted on drawer slides, enabling consistent IMU placement
- Higher rigidity with new structure verified by FEA
- Thruster guards to protect against impacts with walls
- Modular task mechanism mounting
- New task mechanisms, with torpedoes and markers being integrated together
- Smart battery housings
- Adjustable center of mass position by indexing battery rails
- Reduced width, allowing it to fit through a door
- Ergonomic handles for easier transportation
- Anodized for added protection
Read more about these improvements on the Mechanical Team Page
Talos is uses the same Riptide Software stack of all of our previous AUVs. This year a focus was placed on improving the testability of our software systems, with several new systems created for this purpose:
- New editor developed for robot task code to reduce common errors faced during development
- Automated tests written for robot task code to minimize crashes during competition runs
- Improved visualization tools to view and operate the vehicle during pool tests
- Tools to allow vehicle operation without needing command line interface
Read more about the team’s software systems on the Software Team Page
Tempest was our previous AUV, which used the same central housing as Talos. It’s development began in January 2020 and was initially supposed to be designed in 2020, and built throughout 2021 going on to compete in RoboSub 2021. Unfortunately, due to roadblocks put in place by the COVID-19 pandemic, production was delayed leaving Tempest’s first pool test to be February 2022. These problems have only made the team stronger, more creative, and more effective. Tempest is our best robot to date and we are incredibly excited to bring it to RoboSub 2022!
At a glance:
- 6 degrees of freedom/motion
- Dual housing design
- Hot-Swappable battery system
- Chassis can be flat-packed
- Known absolute orientation and depth
- x-y positional location estimates from internal sensor and external environment
- 71 hours spent swimming in pool tests
- ~186 kJ expended per hour swimming
- So far, 7 all-nighters to make it happen
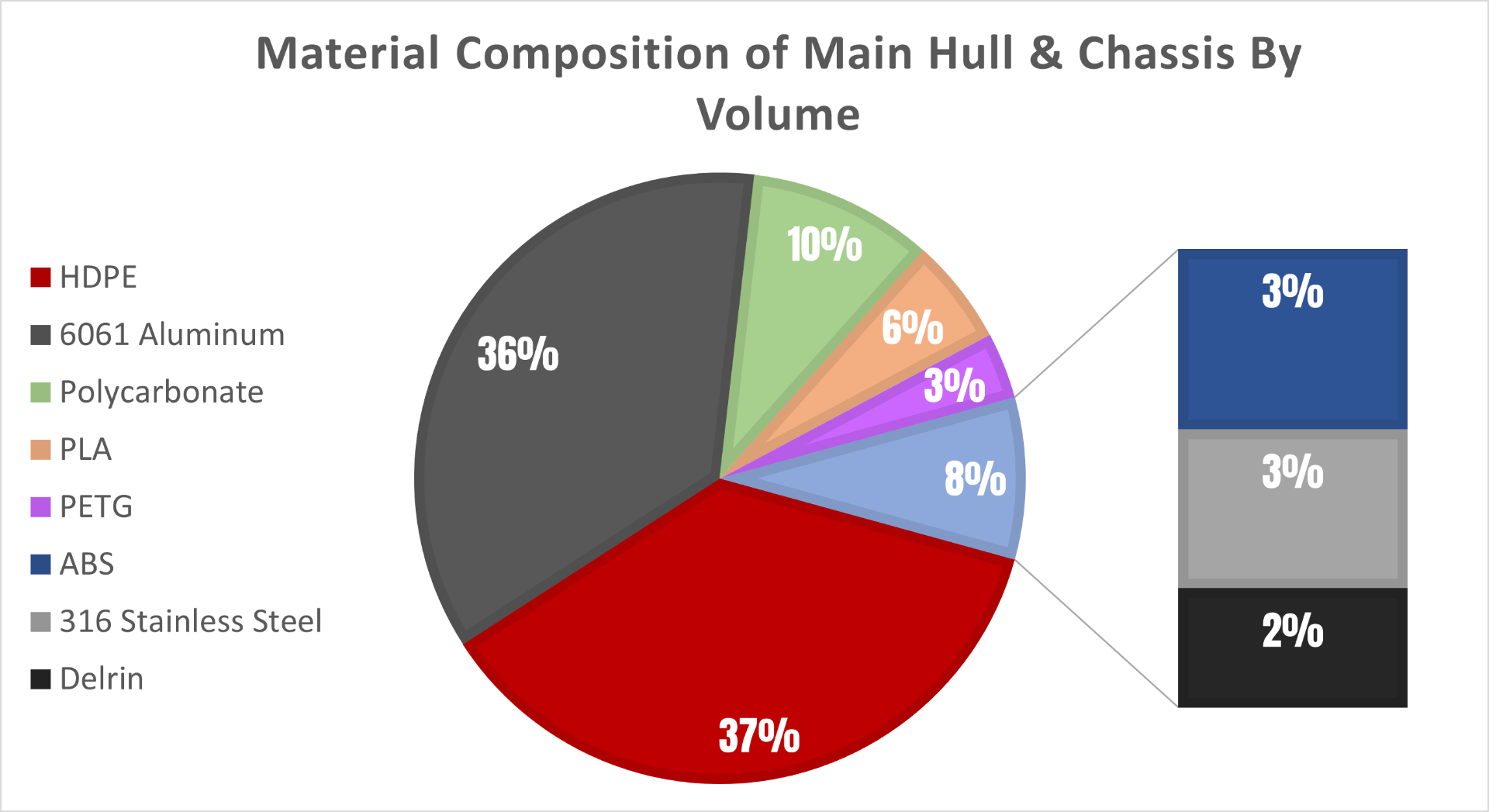
The Mk1 electrical system uses a Backplane/Card design to isolate each function into 4 distinct PCB systems: Power, Electronics Speed Controller (ESC), Actuator, and Coprocessor (Copro). These custom-made cards each serve an integral function for the electronics system of Tempest.
Power Board
The power board is responsible for distributing and regulating power from our MaxAmp Lithium-ion batteries to the rest of the robot. It uses a diode/or controller to balance the batteries. Balancing is necessary in order to avoid back-feeding the batteries, which can not only damage them but also create unsafe conditions.
ESC Board
The ESC board contains one electronic speed controller for each thruster (8 in total). Taking commands from our software controller, it sends the power necessary for Tempest to move to a given location or achieve a certain orientation.
Actuator System
The actuator system is responsible for actuating the various task mechanisms required for competition: claw, torpedo, and marker droppers. The actuator board is a stacked design including a dedicated control board and a custom-designed microcontroller Hardware Attached on Top (HAT). This design was selected due to space constraints within the electronics cage.
Copro Board
The copro board is the primary interface between the main computer and the Tempest’s electronics system by running firmware. It exposes a Micro-ROS node which translates topic messages into electrical signals. Additionally it reports back robot states including battery voltage and internal temperature.
Backplane Board
The backplane board is the primary interconnect for the four individual electrical systems, linking important signals between the various boards.
Our robot uses a variety of sensors to navigate its surroundings. We use an Extended Kalman Filter (EKF) to fuse sensor data together and produce an estimate of Tempest’s current pose.
- Doppler Velocity Logger (DVL) uses the Doppler Effect and gives us velocity along all axes
- Inertial Measurement Unit (IMU) uses magnetic fields to give us specific force along all axes and angular velocity along all axes
- Depth Sensor gives us our Z position in relation to the surface of the water
With our Camera we are able to locate competition objects and aid in countering drift in the robot’s position.
Processing all this information is the NVIDIA Jetson AGX Xavier. It uses a ROS2 codebase to run our controller, process vision, and perform Simultaneous Localization and Mapping (SLAM). It makes its decisions using a BehaviorTree based autonomy system. Using all this Tempest is able to navigate through its environment and choose the best course of action.
Puddles
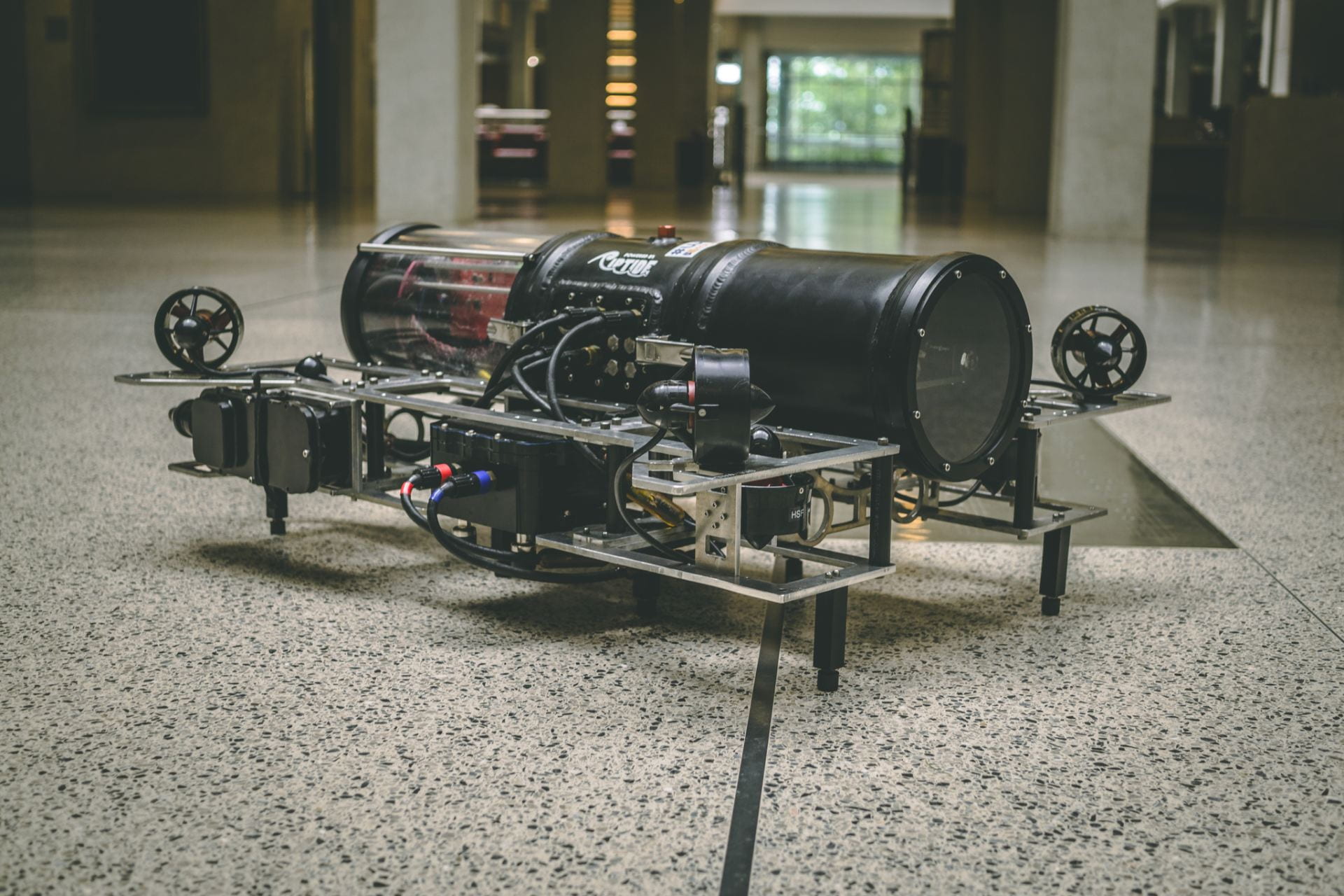
The Underwater Robotics Team’s latest AUV which competed in RoboSub 2019 and placed 11th out of 55 teams. Puddles will compete again in RoboSub 2020. It was developed over the course of the 2018 – 2019 and 2019 – 2020 school years. Puddles was recently revived during the 2022-2023 academic year as a Masters Project. During this project several aspects of Puddles were improved to allow the vehicle to become a research testbed.
At a glance:
- 6 degrees of freedom/motion
- Single housing design
- Hot-Swappable battery system
- Known absolute orientation and depth
- x-y positional location estimates from internal sensor and external environment
- 100+ hours spent swimming in pool tests
- 20+ all-nighters to make it happen
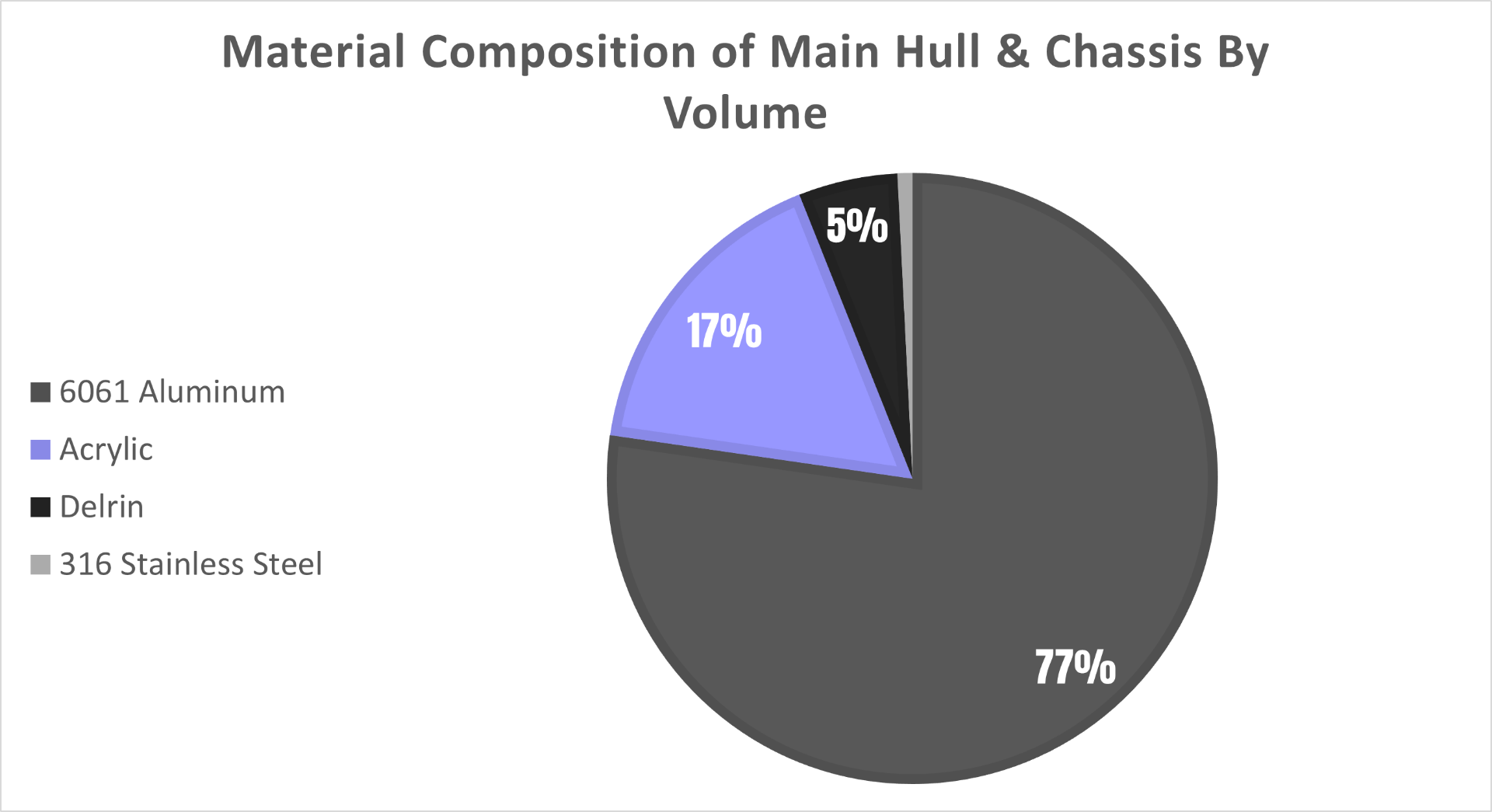
Previous AUVs
Maelstrom - Competed in RoboSub 2018
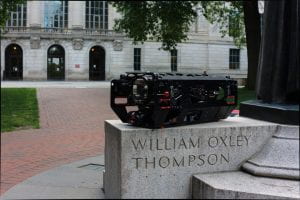
Maelstrom was developed over the course of the 2017 – 2018 school year. It competed in RoboSub 2018, placing 10th out of 47 teams. The vehicle uses the main hull from Riptide but has a completely redesigned chassis. The chassis is a thin aluminum frame wrapped around from enhanced protection.
Click to learn more about the cameras used!
Riptide 2.0 - Competed in RoboSub 2017
A revision of Riptide with the same main hull and a slightly redesigned chassis. It boasted upgraded sensors and maneuverability. Riptide 2.0 completed in RoboSub 2017 and was developed over the course of the 2016 – 2017 school year.
Riptide 1.0 - Competed in RoboSub 2016
UWRT’s premier AUV, competed in RoboSub 2016, and was developed over the course of the 2015 – 2016 school year. The design features a singular main hull with a minimally invasive aluminum chassis for mounting components.
Retired ROVs
Jaws
The team’s last competition ROV, featuring custom thrusters and a large dome for optics.
Block-O-Bot
An ROV full of school spirit. The vehicle made use of a watertight acrylic tube sandwiched between two OSU themed plates. Also featured on the bot is a custom manipulator arm.
Carbon Carmen
As its name would suggest, the Carbon Carmen is an ROV made primarily with carbon fiber. This design decision reduced weight and provided a great wow-factor.
Buckeye Boulder
The robot that started it all! The Buckeye Boulder is an ROV consisting of an open PVC frame that made use of a custom controller. We’ve come a long way since then!